Description & Background
Following the July 1995 failure of a Tainter (radial) gate at the U.S. Bureau of Reclamation’s Folsom Dam in Folsom, California, the dam safety industry placed a renewed emphasis on inspection criteria and performance requirements for gated structures. The 1995 Folsom Dam incident placed much of the industry’s focus on dams with Tainter (radial) gates; however, there are many other types of gates such as vertical lift gates, drum gates, roller gates, and Obermeyer gates. Each gate type and its associated operating systems and machinery present a unique set of challenges for dam owners and operators with respect to operations and maintenance (O&M), inspection, and analysis requirements.
Operations and Maintenance (O&M)
For each gate type, it is important to understand the key structural components, their age, and their intended function or operation. It is likely that design requirements may have changed since the gates were put in place, and thus the existing infrastructure may not meet current the standard of practice. The condition of structural components (e.g., the gate arms, struts, and skin plate) should be regularly observed for signs of overstress, corrosion, fatigue, cracking, or other issues and repaired as needed. For example, excessive vibration during gate operation may lead to increased cyclic loading resulting in fatigue cracking. In addition, welded connections can be more vulnerable to undetected cracking. Gate coatings which are not kept in good condition may also lead to localized corrosion that ultimately could result in the loss of the member’s overall section. Lastly, particular gate types should be operated in accordance with their design intent and function. For example, some gate types are not designed to regulate flows while others are not designed to withstand overtopping, and thus should not be operated in these manners.
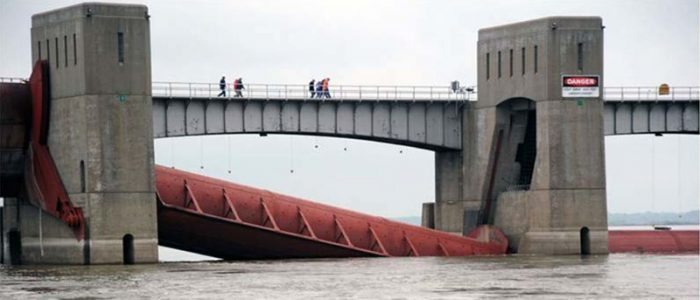
Damaged roller gate at Mississippi River Lock and Dam 25 (2010, Missouri). (Photo Source: US Bureau of Reclamation)
The operating systems (mechanical and electrical) and associated machinery for each gate type are also critical components which must be inspected and maintained in conjunction with the gates themselves. Some gates may be manually operated, such as by hand wheel screw actuators, while others rely on electrically or hydraulically operated systems. If electrical power is required for operation of the gates, an auxiliary/backup power supply (e.g., a gasoline or diesel-powered generator) should be available in case of emergency. Hydraulically operated gate systems require not only electrical power, but also hydraulic fluid and means to transfer the fluid in order to operate the system. Machinery to operate gates also varies, though this typically includes electric motors as well as electric winches or hoists. The type of lifting device may also vary on winches and hoists; wire ropes and chains are most common. Corrosion of lifting chains and uneven tensioning of wire ropes can lead to unsymmetrical lifting loads, which may in turn cause damage to the lifting device or the gate itself. All of these are components which must be included in a robust O&M program that will provide regular upkeep and timely repair of the gates and associated operating systems.
A well-established O&M program should include preventative measures such as painting and lubrication (if applicable) and other periodic repairs to maintain gates and associated equipment in their intended operating condition. This includes ensuring the proper functionality of all electrical and mechanical equipment, as well as instrumentation and surveillance systems such as reservoir level and gate opening indicators which may be monitored by telemetry. Load-testing may be required for standby and backup power sources. For Tainter (radial) gates, specific key maintenance items could include lubrication of the trunnion pins and bearings (if applicable). Note that not all trunnion pins are lubricated; some exhibit bronze bearings while others have graphite bearings. Smaller Tainter gates also exist that are steel on steel with no low friction surface provided. Maintenance procedures should be tailored to the specific gate type(s) at each dam. Maintenance checklists can be utilized to track and document maintenance procedures and protective measures for each gate and its associated systems. All gates should be exercised regularly (either during regular operation or on a test basis) to ensure proper functionality. Tests of gate operation should include use of both primary and auxiliary/backup power systems, if applicable. Records of gate performance and completed maintenance should be maintained for future reference and planning purposes. Each O&M program should be tailored to the specific dam site, as appropriate. O&M procedures should be re-evaluated if project operations change (which may result in changed maintenance requirements).
Inspection
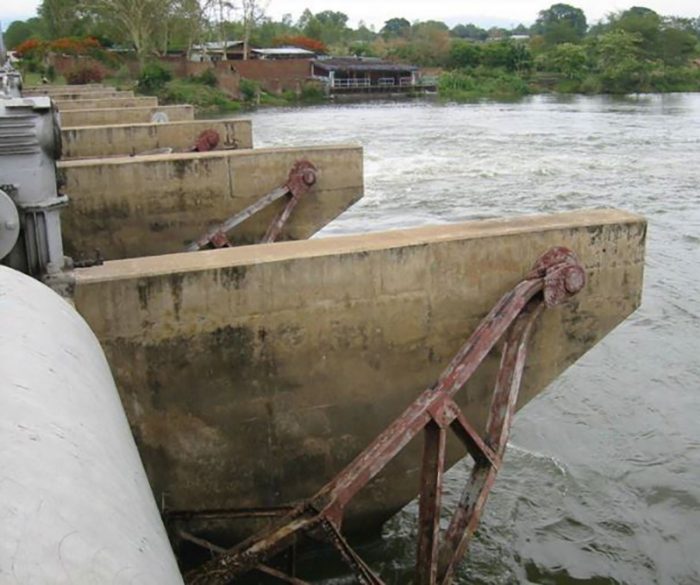
Liwonde Barrage Tainter Gate Failure (Malawi, Africa). (Photo Source: US Bureau of Reclamation)
Regular inspection is another key aspect of safe and reliable operation of gated structures. The type and frequency of inspections may vary based on the gate type(s) and operating systems. Regularly scheduled inspections should include observations of metal and concrete surfaces for signs of abnormal conditions such as deterioration of coatings, damage, cracking, leakage, or other issues. Inspection of mechanical equipment should include observation of valves, pumps, controls, auxiliary equipment, power sources (including backups), and any instrumentation and/or telemetry equipment. Regular inspections should occur on a routine basis appropriate for the size and complexity of the gated structure as part of overall surveillance and monitoring for the dam. Records should be maintained of inspections and equipment testing.
Visual observations of the gates and associated operating systems may also occur informally as part of routine (i.e., day-to-day) operations. Operations personnel should be familiar with the O&M program for each gate and trained to identify developing issues or problems which may require further attention.
Special inspections of the gates and associated operating systems should occur following an extreme flood, significant earthquake, or other unusual event.
Following the 1995 Folsom Dam incident, the Federal Energy Regulatory Commission (FERC) implemented it’s Tainter Gate Initiative which required detailed gate inspections at ten-year intervals for Category I gates. Owners with FERC-regulated dams subject to the Tainter Gate Initiative must submit Detailed Radial Gate Inspection Reports which document the gate inspection, operation tests, load tests on motors and other electrical/mechanical components, and analyses of records. Similar inspection programs have been adopted by other state and federal agencies. These programs can be used to help plan and implement more thorough gate inspections.
Gate inspections may require special procedures and/or advance planning in order to safely observe the structures. This could include the need to plan inspections during maintenance outage windows to allow for dewatering and careful observation of structures. Underwater inspections can also be performed by divers or by video inspection using a remote operated vehicle (ROV). Inspections may require specialized rope-access techniques, confined space entry, and/or the implementation of lock-out/tag-out procedures in order to allow for safe inspection.
Potential Failure Modes and Risk
The potential failure mode analysis (PFMA) process can be used to identify potential failure modes (PFMs) related to gates and other mechanical systems. PFMs can be considered for various loading conditions from normal operating conditions to flood loading. Operational failures (i.e., a failure or inability to operate) can also occur. The PFMA process can be used to help identify data gaps, needed analyses, risk reduction measures, as well as additional surveillance and monitoring which can be implemented to improve the safety and reliability of the gated structure. Operations personnel should provided information regarding any developed, credible PFMs to help guide O&M, inspection, and surveillance and monitoring efforts during routine operations.
The presence of gates at a dam also presents additional risks relative to an ungated structure. This provides the need to develop an understanding of the consequences of gate failure, what reliability and redundancy exists within the system, and what means are available to stop or limit flows in the event of a gate failure. From an operational standpoint, gates may fail to operate as intended, possibly from mechanical or electrical failure, control system failure, or human error. Gates may also be opened inadvertently, resulting in uncontrolled releases which put downstream populations at risk. Alternatively, mechanical equipment may fail due to lack of maintenance and/or changes in operation. Dam owners should work to understand these risks and evaluate means to mitigate them if necessary.
References:
(2) FEMA. (2004). Federal Guidelines for Dam Safety. Federal Emergency Management Agency.
This lesson learned was peer-reviewed by Josh Paquet, Gannett Fleming, Inc.
Summary
Photos
- Failure of Radial Gate No. 3 at Folsom Dam (1995, California). (Photo Source: US Bureau of Reclamation)
- Uncontrolled (sunny day) release from the failed radial gate at Folsom Dam (1995, California). (Photo Source: US Bureau of Reclamation)
- Ulefoss Dam Gate No. 1 Failure (1984, Norway). (Photo Source: US Bureau of Reclamation)
- Liwonde Barrage Tainter Gate Failure (Malawi, Africa). (Photo Source: US Bureau of Reclamation)
- Damaged roller gate at Mississippi River Lock and Dam 25 (2010, Missouri). (Photo Source: US Bureau of Reclamation)
- Fatigue cracking in girder flange at diagonal anchor plate at Markland Lock and Dam (1994, Pennsylvania). (Photo Source: US Bureau of Reclamation)
- Example event tree for mechanical drive failing to open gate. (Photo Source: USACE, Risk Management Center)
- Example event tree for controls failing to open gate. (Photo Source: USACE, Risk Management Center)
Videos
- ASDSO Dam Owner Academy: Operation & Maintenance Plans
- ASDSO Dam Owner Academy: Dam Inspections
- ASDSO Dam Owner Academy: Spillways & Outlet Works
- Folsom Dam Gate Failure
- Developing Operations and Maintenance Manuals for Dams (2014)
- Moment Dam Gate Collapsed at Lake Dunlap
Case Studies
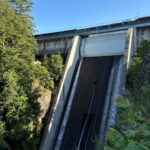
Cleveland Dam (British Columbia, 2020)
Cleveland Dam is a concrete-gravity structure 300-feet-high with a crest 640-feet(or 195m) long. It is located in in North Vancouver, British Columbia, Canada. The dam impounds the Capilano Reservoir which is in one of three major Metro Vancouver watersheds that provide drinking water to the Greater Vancouver region.
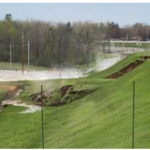
Edenville Dam (Michigan, 2020)
Edenville Dam experienced a static liquefaction instability failure of its downstream slope on May 19, 2020. The resulting breach flow reached and overtopped the downstream Sanford Dam about 2-3 hours later, resulting in failure of that dam as well.

Folsom Dam (California, 1995)
Located approximately 20 miles northeast of Sacramento, California, Folsom Dam was designed and constructed by the U.S. Army Corps of Engineers to generate hydropower along the American River. The 340-foot high concrete gravity Folsom Dam along with two earthen wing dikes...
Additional Case Studies (Not Yet Developed)
- Lake Dunlap Spill Gate (Texas, 2019)
- Ulefoss Dam Gate No. 1 (Norway, 1984)
- Guernsey Dam Drum Gate (Wyoming, 1986)
- Black Canyon Diversion Dam Drum Gate (Idaho, 1998)
- Cresta Dam Drum Gate (California, 1997)
- Greenup Locks and Dam Anchor Arm (Kentucky, 2010)
- Cannelton Locks and Dam Culvert Valve (Indiana and Kentucky, 1999)
- Mississippi River L&D 25 Roller Gate (Missouri, 2010)
- Hoover Dam Drum Gate (Arizona, 1941)
Additional Non-Failure Case Studies
- Liwonde Barrage Dam Tainter Gate Failure (Malawi, Africa) — still in operation in damaged condition
- Markland Lock and Dam Miter Gate Fatigue Cracking (Pennsylvania, 1994)
- John Day Lock and Dam Vertical Lift Gate Fatigue Cracking (Oregon)
Best Practices
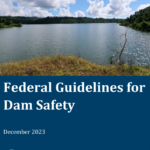
Federal Guidelines for Dam Safety
Author: Federal Emergency Management Agency
Date Published: 2023

Risk Management - Best Practices and Risk Methodology
Author: United States Bureau of Reclamation
Date Published: 2015
Other Resources
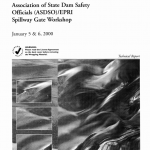
Association of State Dam Safety Officials / EPRI Spillway Gate Workshop
Author: Electric Power Research Institute, Inc. (EPRI)
Technical Report
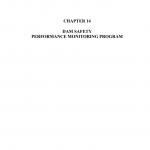
Engineering Guidelines for the Evaluation of Hydropower Projects: Chapter 14
Author: FERC
Dam Safety Performance and Monitoring Program (Revision 3)
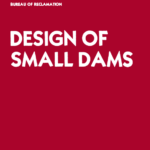
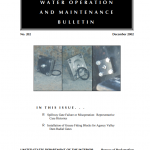
Spillway Gate Failure or Misoperation: Representative Case Histories
Author: W.J. Graham and R.C. Hilldale
Dam Safety Office Report No. DSO-01-01, USBR